Imprimarea 3D a metalelor bazată pe arcul electric este pe cale să transforme radical producția componentelor metalice. Metoda de fabricație aditivă cu sârmă pentru sudare, care urmărește îndeaproape conturul final, aduce obiectele tridimensionale la forma vizată, prin aplicarea strat cu strat a trecerilor. Exemple se pot găsi în domeniul construcţiei de instalaţii, de avioane, al construcției de matrițe sau în domeniul construcțiilor ușoare. Avantajele se manifestă cu precădere în cazul geometriilor complexe, cu o rată de prelucrare ridicată. În acest caz, procesul este mai flexibil și, nu arareori, mai rentabil decât procedeele de prelucrare sau de formare. Avantajele se manifestă și în domeniul pieselor de schimb, al construcției de prototipuri și în fabricația în serie mică. În spațiul american există între timp standarde pentru imprimarea 3D a metalelor, în timp ce în Europa acestea sunt în lucru în ceea ce privește recipientele sub presiune fabricate aditiv, fără expunere la foc. Linde Engineering, MIGAL.CO, TÜV SÜD Industrie Service GmbH și Fronius International au intrat pe scenă cu scopul de a ajuta la succesul definitiv al variantei de fabricație bazată pe sârmă.
Componente personalizate și just-in-time
Adesea, tehnicile clasice de fabricație, cum ar fi turnarea implică și procesul costisitor al construcției de forme și matrițe. La aceasta se adaugă termenele de execuție și costurile de dezvoltare. Dacă o companie alege să mizeze pe imprimarea 3D a metalelor, ea poate scurta în mod hotărâtor ciclurile de producție. Metodele de fabricație aditive favorizează nu doar producția rapidă a componentelor prototip (Rapid Prototyping), ci și fabricarea Just-in-Time. Aceasta înseamnă că ele ajută la evitarea situațiilor riscante de tipul Single-Source – adică dependența de furnizori unici, combinată cu menținerea de stocuri, cu costuri ridicate. În funcție de diversele componente necesare, se aleg „rețetele“ adecvate în software, iar acestea sunt „imprimate“ în funcție de necesități. Nu există aproape nicio limită pentru geometria componentelor. În schimb, topologia și modelele cu flux optimizat ocupă un loc important în producția de zi cu zi în fabricația aditivă – chiar și pentru componente mari.
Procedeul de sudare CMT – ideal pentru imprimarea 3D a metalelor
Imprimarea 3D funcționează cu diferite procedee. Procedeele bazate pe sârmă, cum ar fi „Fronius Additive“, topesc sârma pentru sudare și realizează în acest fel piesa, strat cu strat. Pentru ca în material să nu pătrundă prea multă căldură, ele trebuie executate cu cât mai puțină energie posibil. Adecvat în special pentru imprimarea 3D a componentelor din aluminiu este procedeul de sudare Fronius Cold-Metal-Transfer (CMT), bazat pe procedeul MIG. CMT este un procedeu cu arc electric scurt „mai rece“, care minimizează energia liniară, în ciuda ratei de depunere ridicate. El este excelent pentru sudarea aditivă, unde depunerea ciclică de straturi prin sudare generează o energie liniară ridicată.
CMT suportă funcții care sunt potrivite pentru imprimarea 3D a metalelor. Un exemplu tipic în acest sens îl reprezintă „corecția puterii“. Ea permite adaptarea precisă a puterii electrice utilizate în funcție de faza respectivă a procesului. În tot acest timp, rată de depunere rămâne constantă.
„Prin intermediul funcțiilor noastre CMT-Additive-Pro dezvoltate special pentru fabricația aditivă, cum ar fi corecția puterii sau Deposition Stabilizer, care menține constantă rată de depunere, putem controla în mod precis puterea de intrare și, în consecință, înălțimea și lățimea sudurii“, declară ing. Leonhard Reiter, Fronius R&D.
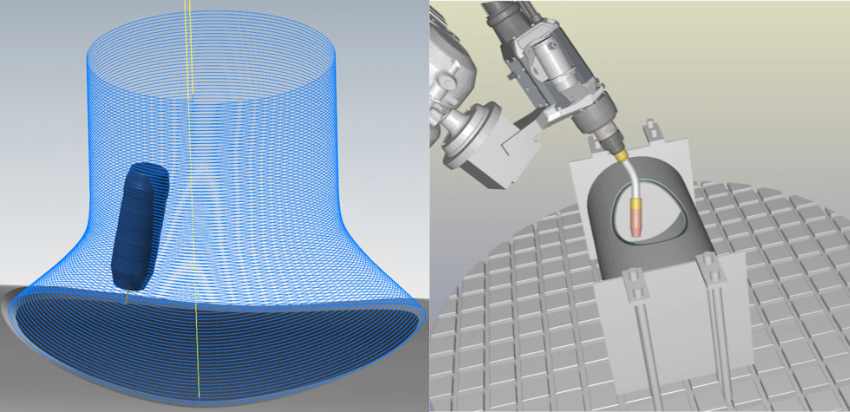
Fronius susține elaborarea standardelor pentru componente și recipiente sub presiune realizate prin fabricație aditivă
În calitate de membru al „Grupului comun de lucru pentru componente fabricate aditiv conform Directivei privind recipientele sub presiune a Institutului German pentru Standardizare (DIN)“, Fronius, în colaborare cu MIGAL.CO, Linde Engineering și TÜV SÜD, a participat la calificarea prototipului unei componente sudate aditiv. În acest context, a fost verificată aplicabilitatea proiectului de standard prEN 13445-14 pentru componente de recipiente sub presiune, fără expunere la foc.
Calificarea materialelor, verificarea proiectului, calificarea procedurii, fabricația aditivă, verificarea componentelor și verificarea sub presiune, precum și documentarea cu exactitate a lanțului de procese, au fost realizate conform competențelor partenerilor implicați, în locațiile corespunzătoare, iar în urma acestora a fost elaborată o Specificație privind procedura de fabricație aditivă – AMPS (Additive Manufacturing Procedure Specification), cu caracter obligatoriu.
„În proiectul de standard prEN 13445-14, precum și în standardul DIN/TS 17026, deja publicat, este luat în considerație întregul lanț valoric, inclusiv toate detaliile de monitorizare. În acest fel este avută în vedere posibilitatea respectării cerinţelor fundamentale de siguranţă prevăzute în Directiva privind recipientele sub presiune 2014/68/UE“, descrie dr. ing. Kati Schatz, Linde Engineering, conținutul standardului aflat în elaborare. „Sunt incluse toate detaliile. Este vorba în special de cerințele privind materialele, proiectarea, calificarea procedurii aditive, producția și verificarea, precum și recepția și documentarea. Nu există aproape nicio diferență între această procedură și cea pentru recipientele sub presiune fabricate în mod convențional. Chiar și în lipsa așa numitei ‚prezumții de conformitate‘ a viitorului standard armonizat, dat fiind ca vor mai avea loc revizii până la finalizare, specificația poate totuși servi ca ghid orientativ tuturor celor implicați în procesul de fabricație aditivă a recipientelor sub presiune.“
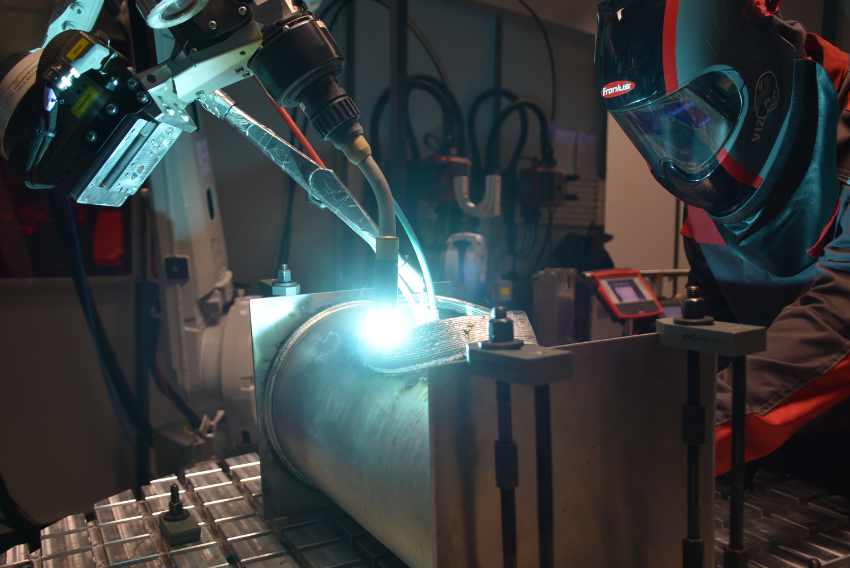
Design, materiale și materiale de adaos
A fost verificat întreg lanțul de procese pe baza unui recipient sub presiune sub forma unei conducte de ramificație. Conform propunerii de design, ramificația (zona aplicată aditiv până la ștuț) a fost realizată pe o conductă principală fabricată tradițional, prevăzută cu decupajul necesar în acest sens. În acest caz vorbim despre o componentă hibridă, deoarece materialul substrat care trebuie sudat devine parte componentă a recipientului sub presiune.
„În ceea ce privește materialul, ne-am decis pentru aluminiu. În construcţiile de instalaţii utilizăm aliajul maleabil auto-călibil datorită rezistenței sale excepționale la temperaturi scăzute, de până la minus 273°C. Sudarea materialului este însă o provocare. Astfel, nu doar alegerea procedeului și a parametrilor de proces sunt decisive pentru obținerea rezultatului dorit, ci și alegerea materialului de adaos“, explică Martin Lohr, Linde Engineering.
Un rol esențial la imprimarea 3D a metalelor îl joacă materialul de adaos: Atât pentru diametru, cât și pentru compoziția chimică, care trebuie să conțină cât mai puțin hidrogen, se aplică toleranțe stricte. În plus, pentru desfășurarea producției fără probleme, sârma trebuie să nu prezinte nici un fel de incluziuni și să fie bobinată în straturi suprapuse exact.
„O importantă temă legată de mediu, relevantă din punct de vedere climatic, este amprenta de CO2 a sârmei pentru sudare“, arată Ing. Robert Lahnsteiner, CEO al MIGAL.CO și completează: „În cazul nostru, ea este de 3,8 kg CO2 per kilogram aluminium, ceea ce înseamnă mai puțin de un sfert din media internațională.“
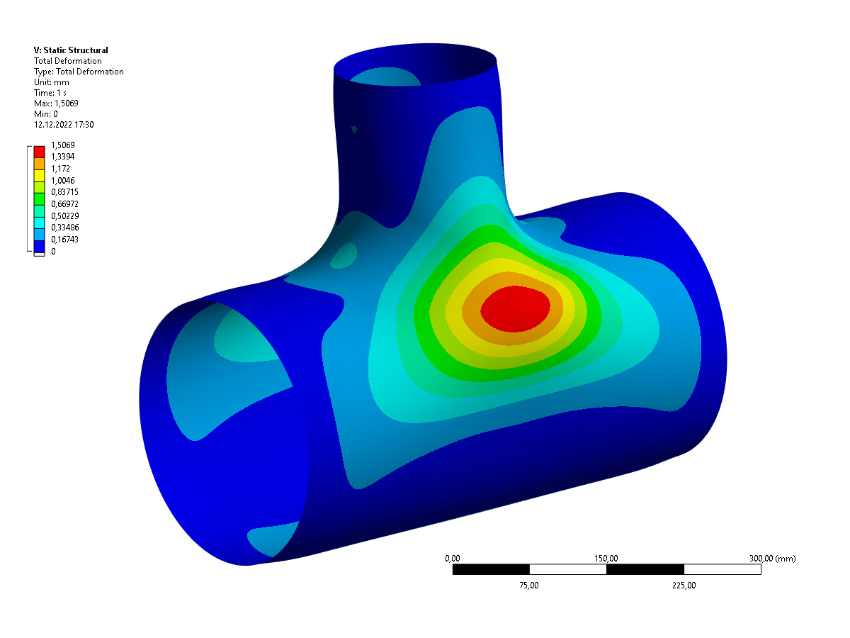
Proiectarea componentei și alegerea procedeului
Trecerea de la conducta de bază a recipientului sub presiune către ștuț a trebuit realizată atât cu optimizarea fluxului, cât și a topologiei. În urma proiectării au rezultat următoarele grosimi de pereți: 8 mm pentru conducta de bază, 14 mm pentru trecerea de la conducta de bază la ramificație și 5 mm pentru ramificație.
Conducta de bază | Trecere | Ramificație | |
Material | EN AW-5083 / AlMg4,5Mn | Al 5183 /AlMg4,5Mn | Al 5183 /AlMg4,5Mn |
Grosime perete / grosime DED [mm] | 8 | 14 | 5 |
Diametru exterior [mm] | 273 | 273 / 168 | 168 |
Material, grosime perete și diametru exterior al conductei de ramificație
Alegerea procedeului DED (procedeu Direct-Energy-Deposition)
Cerințele de bază privind procedeul DED (cunoscut și ca proces Wire-Arc-Additiv Manufacturing) pentru calificarea prototipului de recipient sub presiune au fost după cum urmează:
- rată de depunere cât mai mare posibilă
- procedeu cu căldură redusă, pentru a evita, respectiv a minimiza necesarul de răcire și deformarea
- fără defecte de lipsă de interpătrundere la îmbinarea cu materialul de bază
- insensibilitate la modificări ale distanței pistolet de sudare – piesă
- reproductibilitate absolută a calității ridicate a materialului în limitele calificate ale procedurii Depositing
- adecvare pentru piese de mai mari dimensiuni
Având în vedere cerințele pentru depunerea treptată a straturilor prin fabricație aditivă a fost ales procedeul CMT bazat pe MIG, mai precis CMT mix pentru primul strat și CMT Additive Pro pentru realizarea în continuare a peretelui, în condițiile în care utilizarea corecției puterii a influențat în mod decisiv energia liniară.
Calificarea procedurii
Date fiind diferitele grosimi ale peretelui la nivelul trecerii de la conducta de bază către ramificație, din perspectiva domeniului de valabilitate al prEN 13445-14 au fost necesare trei calificări separate ale procedurii (DPQR). Specificațiile Procedurii de Depunere DPS (Deposition Procedure Specifications) astfel rezultate au caracter de obligativitate pentru procedeul de sudare aditiv. „Rețeta“ finală pentru imprimarea 3D a metalelor, așa numita Additive Manufacturing Procedure Specification (AMPS), cuprinde astfel trei Deposition Procedure Specifications, instrucțiuni privind ordinea de sudare, precum și note privind certificatele materialelor și calificările operatorilor.
„Calitatea constantă a componentelor realizate prin fabricație aditivă este asigurată, pe lângă specificațiile privind tehnica de sudare, de certificatele materialelor și de calificările operatorilor“, explică ing. Manfred Schörghuber, Fronius R&D.
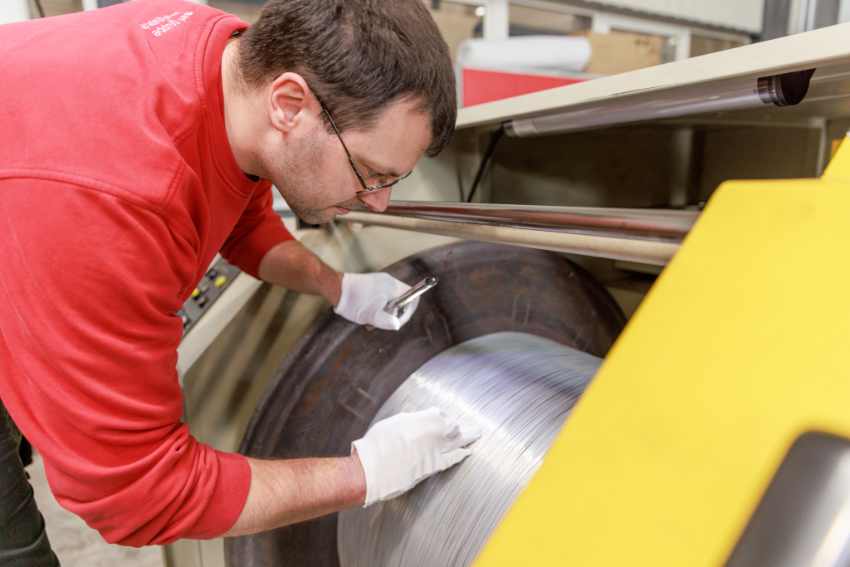
Conform prevederilor din prEN 13445-14, epruvetele individuale au fost supuse la examinări nedistructive și încercări distructive. Pentru a demonstra lipsa defectelor la exterior și la interior au fost realizate examinări vizuale și dimensionale (VT), verificări ale volumului (RT-D) și verificări ale suprafeței (PT) ca procedee de examinări nedistructive.
„Îndeplinirea cerințelor mecanico-technologice privind materialul fabricat aditiv și îmbinarea hibridă am demonstrat-o prin verificări ale compoziției chimice, precum și prin încercări la tracțiune și la îndoire, realizate perpendicular față de direcția de aplicare a straturilor. Apoi, în punctele de start și de stop, precum și la îmbinarea hibridă am efectuat analize metalografice“, relatează ing. (FH) Martin Boche, TÜV SÜD.
Planificarea și simularea traiectoriei robotului
Planificarea traiectoriei pentru aplicația de sudare robotizată a fost realizată pe o conductă de ramificație modelată tridimensional în software-ul CAM (Computer Aided Manufacturing Software) dezvoltat de Fronius.
„Propunerea de modelare aditivă – programul de sudare efectiv – am calculat-o prin introducerea înălțimii straturilor, a poziției, a vitezei și a strategiei de modelare. Traiectoria sudării a fost vizualizată într-o celulă de sudare robotizată modelată de software-ul nostru“, continuă ing. Leonhard Reiter, Fronius R&D.
Detectarea poziției și deplasarea senzorilor
Pentru ca piesa să poată fi poziționată perfect și să se poată interveni pentru corectarea toleranțelor de fabricație, piesa a fost scanată cu Fronius WireSense. Sistemul inovator de senzori utilizează sârma pentru sudare ca senzor tactil și scanează conturul de sudare punct cu punct. Când capătul electrodului atinge suprafața rezultă un scurtcircuit, care declanșează un semnal de distanță, acesta fiind transmis robotului de sudare. Software-ul acestuia compensează valoarea de referință programată offline cu valoarea efectivă a cursei WireSense și corectează, dacă este necesar, traseul de sudare pentru fabricația aditivă. Imediat apoi sârma se deplasează înapoi și – în timp ce robotul continuă deplasarea pistoletului de sudare – din nou înainte către următorul punct. Acolo este declanșat un nou scurtcircuit, este generat un semnal de distanță și, dacă este necesar, traiectoria sudării este modificată încă o dată. În acest fel sunt minimizate abaterile geometrice.
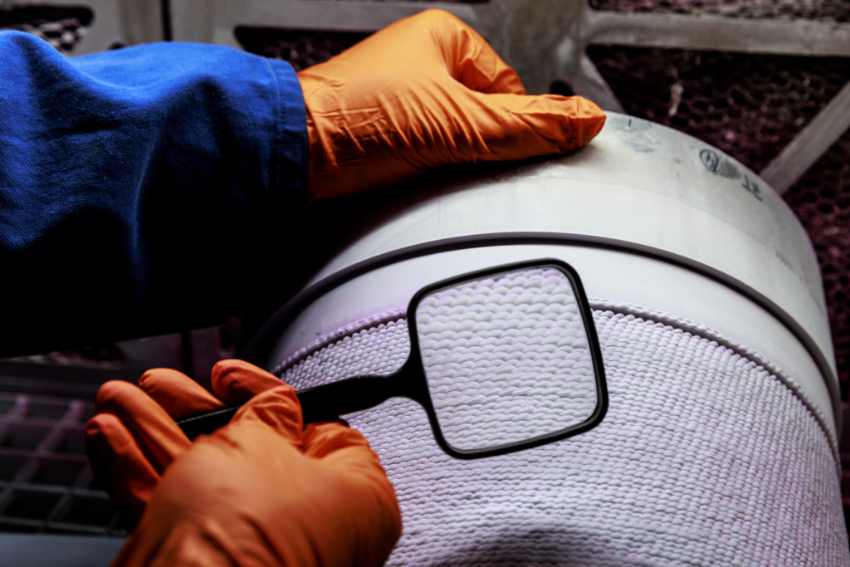
Fabricarea piesei
Diversele grosimi ale peretelui la trecerea către ramificație au putut fi realizate prin amplitudini de pendulare de mărimi diferite. Pentru racordarea optimă necesară de la o trecere la alta și umectarea unitară a marginilor sudurii a fost necesar managementul constant al căldurii. În acest sens, au fost utilizate job-uri de sudare specifice straturilor, cu parametri speciali.
În timpul procesului de sudare piesa a fost dotată cu un circuit de tur și retur de apă. Nivelul de apă astfel rezultat a trebuit să rămână la o distanță suficientă de locul sudării, pentru ca temperatura între treceri să poată fi menținută în domeniul calificat. Acest lucru a permis sudarea continuă, fără pauze de răcire. Prin răcirea piesei a fost minimizată deformarea piesei și a crescut rata de depunere.
„Am observat depunerea straturilor cu o cameră a cărei declanșare a fost sincronizată cu desfășurarea procesului. În acest fel, am putut ulterior să analizăm mai amănunțit abaterile care au intervenit în proces“,completează Reiter, Fronius R&D.
Monitorizarea parametrilor și documentare
Software-ul pentru managementul datelor de sudare, WeldCube a monitorizat limitele parametrilor prestabilite în AMPS (Additive Manufacturing Procedure Specification) și a emis imediat avertizări la depășirea acestora. Din suma tuturor parametrilor a rezultat o „amprentă“ („fingerprint“) a modelării aditive, simplificând analiza posibilelor discontinuități.
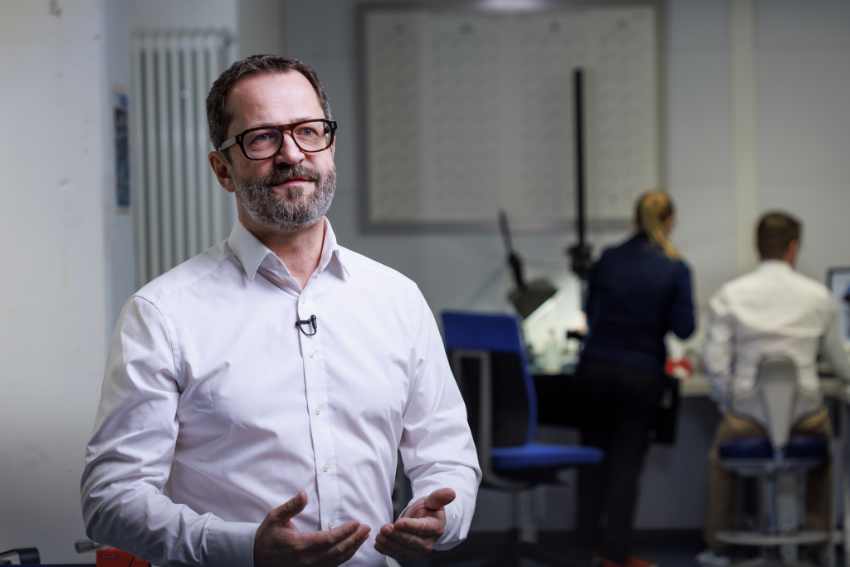
Verificare finală a piesei și perspectivă
Verificarea finală, inclusiv certificarea conformității CE, a fost realizată de către organismul notificat 0036 al TÜV SÜD Industrie Service GmbH. În cazul de față, de la un material de pornire cu date mecanice într-un viitor standard european armonizat (proiectare “armonizată“) și o piesă din clasa de design DC1, a rezultat un volum de verificări al piesei în conformitate cu tabelul următor:
Tipul verificării | Procedură de verificare | Amploarea verificării |
Examinare nedistructivă | Verificarea volumului (RT sau UT),Verificarea suprafeței (VT și PT) | Per piesă 100 % din secțiunile relevante de proiectare (sau 20 % dacă se utilizează un raster adecvat care acoperă complet secțiunea) |
Încercare distructivă | Analiză chimică Încercare la tracțiune pentru determinarea rezistenței și a alungirii la rupereÎncercare la îndoire | 1 x în secțiunea fabricată aditiv 2 x în direcție defavorabilă și suplimentar în secțiunea hibridă 2 x în direcție defavorabilă și suplimentar în secțiunea hibridă |
Verificare finală | Probă de presiune cu apăÎncercare la explozie (efectuată opțional) |
„În paralel cu aceste verificări am realizat analize metalografice, care au acoperit în special acele secțiuni unde s-au constatat imperfecțiuni. Au fost vizate și zonele de trecere dintre materialul clasic și cel realizat prin sudare aditivă, zona hibridă. Analiza metalografică servește în primul rând verificării datelor colectate din monitorizarea parametrilor, precum și din verificarea mecanico-tehnologică și din examinarea nedistructivă. Astfel, sunt prelevate prin sondaj probe care permit concluzii privind măsura în care materialul și procedura de fabricație utilizată sunt lipsite de probleme“, explică Boche.
Prin finalizarea procedurii de evaluare a conformității în acord cu Modulul G al Directivei europene privind echipamentele sub presiune 2014/68/UE, sub forma unei „Calificări a prototipului“ pentru un recipient sub presiune realizat prin fabricație aditivă cu acordarea ulterioară a marcajului CE pentru certificarea îndeplinirii cerințelor acestei directive, Grupul comun de lucru pentru recipiente sub presiune al Institutului German pentru Standardizare (DIN), reprezentat de Linde Engineering, TÜV-SÜD Industrie Service GmbH, MIGAL.CO și Fronius, a dorit să crească gradul de acceptanță al fabricației aditive, în general și în domeniul construcției de instalații și recipiente, în special.
„La final, putem constata cu certitudine că experiența de decenii în procedee de sudare bazate pe arc electric – combinată cu procedee stabile și inovatoare, cum ar fi Fronius CMT Additive Pro – susțin ideea utilizării mai pronunțate a imprimării 3D a metalelor în domeniul construcției de instalații și recipiente. În primul rând, din perspectiva beneficiilor conexe, cum ar fi optimizarea topologiei, fabricarea Just-in-Time sau independența de furnizori, obținem astfel avantaje competitive“, rezumă Schörghuber.
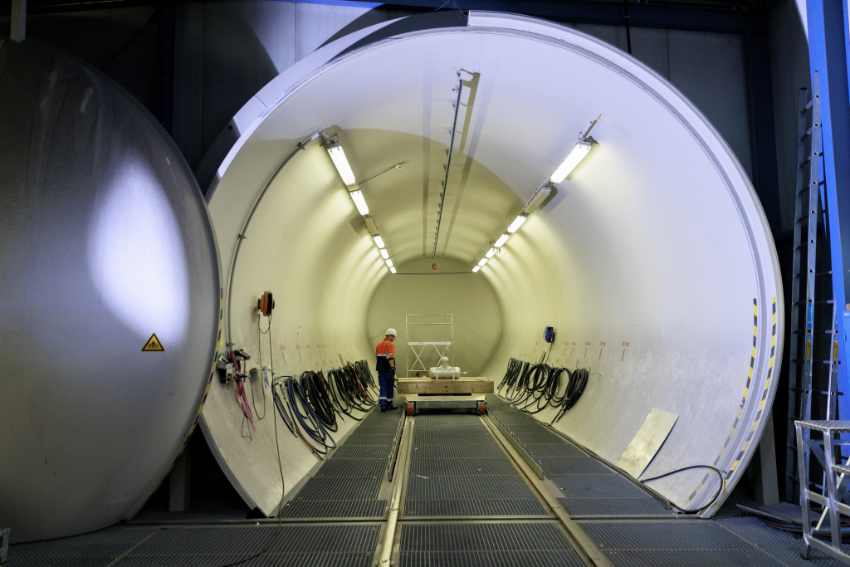
Informații detaliate referitoare la calificarea prototipului sunt disponibile în următorul film documentar:
Fronius eliberează potențialul de sudare al clienților
Cine dorește să se convingă de oferta completă 3D, are această ocazie între 19 și 22 noiembrie 2024 la Formnext în Frankfurt am Main, Standul C99, Hala 12.0, sau la târgul ADIPEC în Abu Dhabi, între 4 – 7 noiembrie 2024, hala 14, standul 14316. Experții Fronius sunt încântați să vă prezinte personal noile oferte și posibilități. Toate persoanele interesate care doresc să profite de know-how-ul Fronius în domeniul imprimării 3D și în soluționarea provocărilor de sudare complexe, se pot adresa specialiștilor din centrul de prototipuri Fronius.
Mai multe despre Fronius Additive Pro găsiți aici.
Informații despre centrul de prototipuri găsiți aici.